Oltre la Lean Production: il Lean Product Development
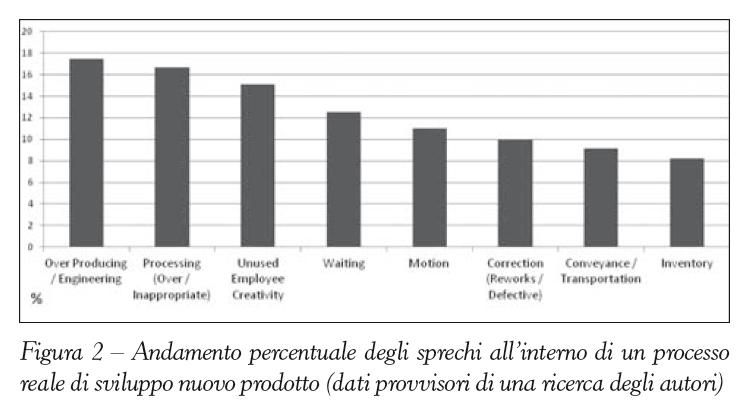
- Chief Engineer. È un ruolo aziendale che assume importanza significativa all’interno di un processo di sviluppo nuovo prodotto che vuole tendere alla massima efficienza. Nell’esperienza Toyota, è una figura altamente tecnica che cerca di capire al massimo il consumatore, sviscerandone i più nascosti desideri e diventandone la “voce” in azienda, fissando gli obiettivi progettuali, oltre che i target di valore e di performance. Non è un mero program/product manager, ma è un decisore fondamentale, che parte dall’elaborazione del concept di prodotto e governa l’intero progetto di sviluppo. In letteratura, è stato spesso definito “super ingegnere”, personaggio chiave per il processo innovativo.
- Quality Function Deployment (Qfd), detto anche House of Quality: è una matrice che mappa i requisiti del cliente (pesati in termini di importanza per il cliente stesso) rispetto a un elenco di attributi di prodotto (attributi tecnici che guidano le performance del prodotto). È uno strumento che supporta la progettazione in modo strutturato, basandosi sulle reali necessità ed esigenze del cliente, convertendo la “voce del consumatore” in un insieme di caratteristiche che l’organizzazione può utilizzare per riconoscere e ordinare le proprie priorità e per aiutarsi nel processo decisionale. L’evidenza empirica dimostra come l’uso di tale matrice comporti risultati positivi in termini di time-to-market, riduzione di costi del prodotto e di soddisfazione delle esigenze dei clienti;
- Regole di Design for X (Dfx), costituisce un’ampia collezione di linee guida da utilizzare durante la fase di progettazione. Le linee guida stesse sono una forma esplicita di conoscenza da utilizzare per controllare, migliorare e intervenire sulle caratteristiche di un prodotto. Le regole di Dfx “obbligano” i progettisti a considerare (e ottimizzare) una serie di aspetti/elementi riguardanti le diverse fasi della vita di un prodotto, come la sua produzione/assemblaggio (Design for Manufacturing/Assembly), la manutenzione e l’assistenza che dovrà subire (Design for Maintainability/Serviceability), il suo smaltimento (Design for Dissassembly/for Recyclability), come anche alcune prestazioni salienti, come la qualità (Design for Quality) o l’impatto ambientale (Design for Environment);
- Tra le regole di progettazione, occorre citare anche il metodo Poka-yoke, letteralmente “a prova d’errore”. È una tecnica, nata in Toyota, che mira a ottenere un processo privo di parti difettose generate, eliminando in questo modo la necessità del controllo qualità. Con tale scelta progettuale si cerca di porre dei limiti al modo in cui un’operazione può essere condotta, forzando l’utilizzatore a una corretta esecuzione della stessa. Lo scopo è appunto quello di evitare (yokeru) gli errori di distrazione (poka), spingendo gli operatori a focalizzarsi su quelle attività che creano valore piuttosto che dedicarsi al monitoraggio.
- I progettisti, nel proprio compito di trovare soluzioni a problemi, sviluppano conoscenza, lungo un ciclo (personale e di gruppo) di apprendimento. Seguendo la ruota Pdca di Deming, è possibile strutturare il processo di apprendimento di un team di progetto, secondo i passi Lambda: Look, controlla ogni azione, processo o informazione in prima persona; Ask, cerca di arrivare alla causa-radice del problema; Model, usa simulazioni o prototipi; Discuss, comunica con i colleghi (progettisti, manager, ecc.); (v) Act, testa sperimentalmente il tuo sapere;
- Il processo così strutturato deve essere opportunamente documentato. Toyota ha sviluppato il metodo standard dell’A3 Sheet (Foglio A3). Fisicamente, ogni progetto è documentato tramite un report breve (per l’appunto un foglio A3, di dimensioni 297 cm per 420 cm), allo scopo di restituire una sintesi di un problema presentato in maniera visiva, che può essere usato per favorire uno scambio di conoscenza e informazioni. Un solo foglio A3 risulta più efficace di un lungo report descrittivo in cui i punti salienti rischiano spesso di essere persi a causa della grande mole di informazioni contenute. L’aspetto innovativo e interessante di tale strumento è non tanto il formato A3, quanto la rappresentazione delle informazioni in tale modo visivo e condensato;
- Per agevolare la comunicazione intra-team e anche intra-progetti, è possibile ricorrere a un’Obeya Room, fisicamente una stanza interamente dedicata alla rappresentazione visiva dell’avanzamento dei progetti, contenente al suo interno fogli A3 e altri tipi di visualizzazione. Tra questi possono poi essere costruite delle matrici, che intersecano le responsabilità individuali dei progettisiti con gli intervalli di tempo, originando scadenze univocamente associate a ogni persona, trascritte su semplici post-it. Diverse esperienze industriali hanno dimostrato come questo tipo di visualizzazione aiuti a condividere le informazioni e a trovare le soluzioni ai problemi, creando consapevolezza su che particolari azioni verranno eseguite e da chi.
- Over-production/Over-engineering: progettare in eccesso oppure in anticipo rispetto alle aspettative del progetto stesso. È uno spreco molto comune laddove i processi di sviluppo non sono sincronizzati tra le funzioni aziendali e tra i diversi attori coinvolti nel progetto;
- Waiting: attese per mancanza di informazioni o decisioni fondamentali e necessarie per proseguire il proprio lavoro. I progettisti si trovano molto spesso bloccati da una lacuna e/o mancanza informativa, magari dovuta a una specifica incompleta o poco chiara fornita da un’altra funzione aziendale;
- Transportation: trasferimento di informazioni da un sistema all’altro. Ancora oggi, i diversi sistemi Ict che supportano la progettazione sono spesso difficilmente compatibili e diverse ore vengono spese per la sola transcodifica dei diversi formati file (es. formati file Cad).
- Processing (Over/Inappropriate Processing): si ha quando si compiono azioni non necessarie durante lo svolgimento di un particolare task, oppure si esegue un task non necessario. Ad esempio, non sono rari i casi di progetti condotti partendo da informazioni (ad esempio specifiche) errate e/o incomplete, che devono essere successivamente rivisti alla luce di un aggiornamento/correzione delle fonti originarie;
- Inventory: accumulazione di eccessive informazioni non utilizzate o che restano in coda a lungo in attesa di essere processate. Caso tipico in cui studi o documenti vecchi rimangono inutilizzati, dopo aver consumato molte ore rilevanti nelle attività di progettazione;
- Defects and Corrections: correggere errori commessi in fase di progettazione e individuare problemi di qualità sul prodotto. È uno spreco anche realizzare un prodotto non di successo, che non soddisfa tutte le richieste del cliente, o che le soddisfa in maniera adeguata (di fatto un prodotto progettato male);
- Motion: eccesso di attività eseguite durante un determinato task, come ad esempio report ridondanti, meeting e review di progetto non necessari;
- Underutilized people’s abilities: mancato utilizzo delle capacità delle persone, insufficiente condivisione di conoscenza tra gli ingegneri, incapacità di creare motivazione o cattiva comunicazione con i fornitori. La progettazione è un processo creativo, cognitivo, che mira a essere innovativo. Ogni mancanza nello sviluppo di queste caratteristiche è uno spreco: disporre di ingegneri non motivati che autolimitano la propria capacità propositiva corrisponde a buttar via preziose risorse non creando valore per il cliente.
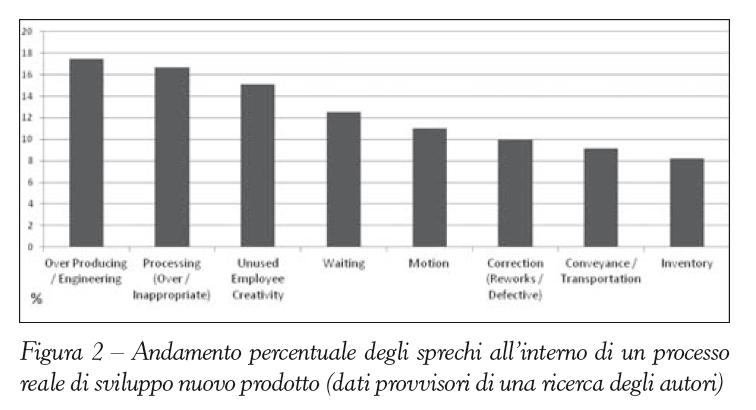
Pagina