Oltre la Lean Production: il Lean Product Development
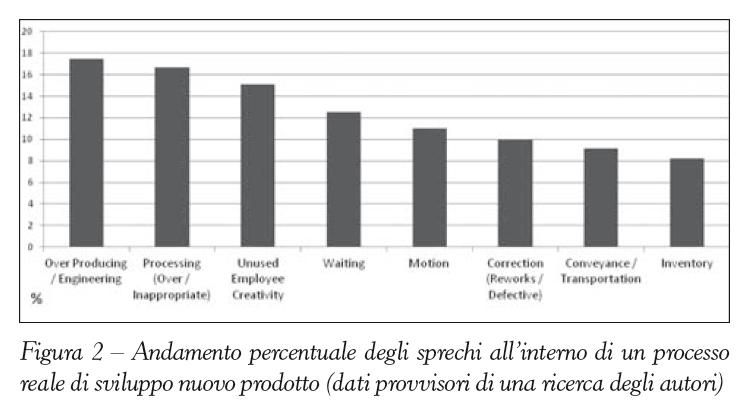
A cura di:
Monica Rossi, Politecnico di Milano, Dipartimento di Ingegneria Gestionale
Sergio Terzi, Università degli Studi di Bergamo, Dipartimento di Ingegneria industriale
Lean Thinking
Il nuovo paradigma industriale introdotto dal lean è basato sulla creazione di valore per il cliente, ossia tutto ciò (risorsa, processo o azione) per il quale il cliente stesso è disposto a pagare. Al contrario, tutto quello che non concorre alla creazione di valore è considerato spreco (muda in giapponese e waste in inglese) e, pertanto, va eliminato dal processo che deve risultare reattivo, veloce, essenziale, per l’appunto “snello”. La logica basilare del lean è quella di creare valore con meno sforzo possibile in termini di tempi e costi, usando il minimo delle risorse necessarie, cercando di azzerare le scorte e mantenendo un elevato livello qualitativo, per fornire al cliente esattamente ciò che vuole, quando lo vuole e nella quantità desiderata. Questo concetto è riassunto in cinque – ormai famosi – principi che stanno alla base del “pensiero” lean:
- Identificare il valore: specificare correttamente cosa abbia valore per il cliente finale, in termini di specifico prodotto con determinate caratteristiche, offerto in un certo momento e a un dato costo;
- Identificare il flusso del valore: individuare l’intero flusso del valore allineando le attività che creano valore nella giusta sequenza, mappando il flusso in termini di materiali e informazioni, rimuovendo tutti i passi che non concorrono alla creazione di valore, ma anzi creano muda/waste;
- Far scorrere il flusso del valore: eseguire le attività a valore in modo continuato, senza interruzioni, per ridurre drasticamente il tempo d’attraversamento di prodotti e informazioni;
- Permettere al cliente di tirare il processo: progettare e produrre solo quello che vuole e quando lo vuole, piuttosto che “spingere prodotti” basandosi su previsioni e stime;
- Puntare alla perfezione: ricercare la perfezione in ogni momento, cercando di rimuovere ogni possibile causa di spreco. La perfezione è in realtà irraggiungibile, proprio per questo non ci si può mai rilassare e va attuato un processo di miglioramento continuo.
- Concurrent Engineering (Ce), è un approccio sistematico – per la prima volta definito a fine degli anni ‘70 negli Stati Uniti – alla progettazione integrata dei prodotti e dei loro processi produttivi e di assistenza post vendita, che costringe alla considerazione di tutti gli elementi del ciclo di vita del prodotto, dal concept alla dismissione. Con il Ce si sviluppa un meccanismo organizzativo che facilita l’integrazione delle diverse funzioni aziendali che devono interagire per sviluppare e introdurre un prodotto nel mercato. Con il Ce, si opera con Team Interfunzionali, minimizzando così errori e mancanze di comunicazione e incoraggiando la nascita di comunicazioni informali. Team con differenti background favoriscono l’ampliamento della base di conoscenza e fanno sì che il progetto possa attingere a più fonti. Nel team devono essere coinvolti fin dalle primissime fasi di sviluppo i fornitori selezionati, con cui condividere informazioni rilevanti (come specifiche, costi, tecniche produttive e ritorni economici) per attuare virtuosi circoli di coinvolgimento e miglioramento continuo;
- Set Based Concurrent Engineering (Sbce), è un metodo di progettazione che si basa sulla logica del Ce, integrando le diverse funzioni aziendali in fase di progettazione. Tipico del processo di sviluppo di Toyota, questo approccio richiede la generazione simultanea di un ampio spettro di alternative (es. componenti per un dato prodotto), che vengono sviluppate e prototipate contemporaneamente. Ogni soluzione è poi gradualmente rifinita o eliminata lungo il processo, durante il quale vengono considerate possibili combinazioni dei componenti in differenti modi, creando così una regione di soluzioni ammissibili. Anzichè quindi essere definita inizialmente e a priori, la configurazione di sistema evolve grazie a “combinazioni creative” delle varie soluzioni, via via eliminate fino ad arrivare alla soluzione finale (Figura 1). Questo comporta la creazione di una grande quantità di informazioni che non verranno subito sfruttate. Le alternative scartate, infatti, avranno generato della conoscenza che non aggiunge direttamente valore al prodotto, ma sicuramente è importante e riutilizzabile per facilitare la progettazione di prodotti futuri.

Pagina
articolo, clienti, inefficienza, lean, lean product development, lean thinking, Monica Rossi, muda, prodotto, Produzione, Sergio Terzi, spreco, sviluppo, valore