Migliorare le performance dei processi di servizio attraverso il Lean Thinking
A cura di:
Roberto Bugatti, Mba Bocconi, esperto di Service Management, è Lean Management docente e ricercatore presso Liuc Ricerca e Formazione – la Business School dell’Università Carlo Cattaneo
Attilio Ragusa, Laurea in Economia e Commercio – Bocconi, esperto di Manufacturing e Lean Management. Consulente di direzione in numerosi progetti per l’implementazione del lean sia in ambito manifatturiero, sia in imprese di servizi
Lean Thinking: moda manageriale o opportunità?
Negli anni ‘90, il Lean Thinking si è affermato nel mondo industriale, partendo dal noto libro di Womack e Jones: “La macchina che ha cambiato il mondo”, che ha concettualizzato il modello sviluppato dagli ingegneri giapponesi via via che è stato implementato il modello produttivo Toyota (Toyota Production System). Questo modello di gestione è stato per un certo tempo guardato con scetticismo nel mondo occidentale, adducendo il motivo che alcuni principi fossero applicabili solo in Giappone, grazie alle particolari caratteristiche culturali di quel paese. Nel tempo, tuttavia, si è moltiplicato il numero di aziende che ha adottato i principi di gestione applicati in Toyota. Inizialmente, tale diffusione ha coinvolto il settore automotive e via via si è esteso dapprima nel resto del mondo industriale e da qualche anno ha trovato applicazioni anche nel mondo dei servizi.
Ma quali sono le ragioni di fondo che hanno favorito il suo successo? A nostro avviso le motivazioni possono essere ricondotte almeno a due aspetti fondamentali:
1. Il Lean Thinking è orientato per sua natura al concetto di valore, inteso come ciò che il cliente desidera (e che è disposto a pagare!). Il Lean Thinking è pertanto per sua natura coerente con le moderne strategie di mercato, che mettono al centro dell’attenzione il singolo cliente e le sue esigenze;
2. Il Lean Thinking scardina il paradigma secondo cui le performance di costo, qualità e servizio hanno una correlazione inversa: secondo tale assunto, non si potrebbe migliorare le condizioni di servizio (qualità e/o consegna) al cliente senza un aggravio dei costi sostenuti e, quindi, in linea di principio, senza richiedere a parità di margine una maggiorazione di prezzo al cliente.
Il Lean Thinking si afferma quindi come metodologia in grado di agire sul livello di soddisfazione del cliente (attraverso radicali miglioramenti di qualità e servizio) e, contestualmente, migliorare l’efficienza interna (attraverso la lotta e riduzione di ogni forma di spreco).
Le aziende che hanno intrapreso l’applicazione dell’azienda snella industriale sono riuscite a raggiungere un positivo riposizionamento di mercato, testimoniato da una maggiore soddisfazione dei propri clienti e l’aumento della penetrazione di mercato, e incrementare radicalmente l’efficienza, ottenendo il miglioramento della redditività grazie a una riduzione dei costi. L’opportunità per le aziende, sia industriali sia di servizio, è quindi di avviare un percorso di cambiamento (più o meno graduale) in grado di influenzare significativamente il conto economico dell’azienda, sia attraverso l’aumento dei ricavi, sia attraverso la riduzione sistematica dei costi operativi.
Applicabilità nelle aziende di servizio e nei processi ‘non-manufacturing’
La filosofia del Lean Thinking è riassunta da Womack e Jones come segue: “… è un modo di fare di più con sempre meno (meno risorse umane, meno attrezzature, meno spazio), avvicinandosi sempre di più al cliente e offrendogli esattamente quello che vuole”. Al di là dell’enunciazione, che rischia di trasformarsi in uno slogan, il Lean ha sviluppato una solida metodologia fatta di principi, di tecniche per il ridisegno di processi e sistemi gestionali, di strumenti per il miglioramento fornendo, a chi decide di intraprendere il percorso di implementazione dell’organizzazione snella, una vera e propria cassetta degli attrezzi.
Le motivazioni che hanno spinto le aziende ad abbracciare l’approccio Lean sono diverse. A nostro avviso ci sono almeno tre aree di risultato che un’azienda di servizio può proporsi di ottenere con la Lean e che possono costituire lo stimolo per intraprendere questo tipo di percorso:
• Riduzione dei costi operativi;
• Miglioramento del servizio al cliente;
• Miglioramento organizzativo interno.
Riduzione dei costi operativi
Uno degli elementi che caratterizzano la metodologia Lean, forse quello più noto, è la ricerca sistematica degli sprechi e la loro eliminazione (o riduzione drastica). L’approccio si contraddistingue, in primo luogo, per la definizione che viene data di spreco (in giapponese: ‘Muda’), ovvero qualsiasi cosa che non aggiunge valore direttamente al servizio o non contribuisce alla realizzazione del servizio. In questo modo molte delle attività accessorie finalizzate al funzionamento aziendale o delle condizioni operative ritenute in genere necessarie costituiscono, in ottica cliente, degli sprechi. La riduzione degli sprechi non è vista fine a se stessa, ma come mezzo per garantire al cliente un servizio migliore a prezzi più competitivi: nella filosofia Lean, i benefici prodotti dalla caccia agli sprechi, per essere realmente tali, devono essere ribaltabili sul cliente.
Secondo il modello di riferimento proposto da Womack e Jones nel loro testo, gli sprechi dei processi possono essere classificati in sette differenti tipologie (vedi Fig. 1).
Nelle applicazioni dell’approccio Lean alle aziende di servizio si è soliti aggiungere un’ottava tipologia.
1) Processing. La prima categoria di spreco è costituita dalle lavorazioni superflue, che si possono manifestare sotto forma di:
• Duplicazione di attività che generano output equivalenti (per es., elaborazioni che producono lo stesso tipo di informazione);
• Raccolta e organizzazione di dati non utilizzati (per es., report che non risultano utili a nessuno);
• Autorizzazioni superflue (per es., visti autorizzativi non associati a effettiva attività di controllo). • In ottica di riprogettazione del processo, le lavorazioni superflue andranno eliminate.
2) Correction. La seconda categoria di spreco è costituita dalle rilavorazioni che sono rivelatrici della bassa ‘solidità’ del processo, cioè della sua incapacità di intercettare la difettosità nel momento in cui si manifesta, lasciando che questa comprometta il servizio finale. Tipiche rilavorazioni che si presentano negli uffici sono:
• Correzioni di errori nei documenti (per es., l’inserimento di un’anagrafica errata si traduce nella presenza nel Database clienti di più riferimenti per lo stesso soggetto, che comporterà una difettosità nel momento di avvio di una campagna di Direct Marketing);
Nel tempo, il mondo delle imprese ha applicato filosofie gestionali e strumenti per migliorare le proprie performance. Tali applicazioni sono sempre state strumentali al raggiungimento di miglioramenti imposti dalle condizioni di mercato. Gli anni ‘70 e gli inizi degli anni ‘80 sono stati caratterizzati dall’esigenza di conseguire miglioramenti significativi dell’efficienza, che nel mondo industriale è culminata nei progetti di automazione anche molto spinta (Computer Integrated Manufacturing) e nei servizi ha visto la revisione e informatizzazione delle procedure. Dalla seconda metà degli anni ‘80 è cresciuta l’attenzione per il cliente, prima attraverso un rinnovato interesse verso la qualità, successivamente attraverso la ricerca del miglioramento radicale del livello di servizio al cliente (riduzione drastica dei tempi di consegna con l’utilizzo del Just in time). Negli anni ‘90 è nato il Lean Thinking.
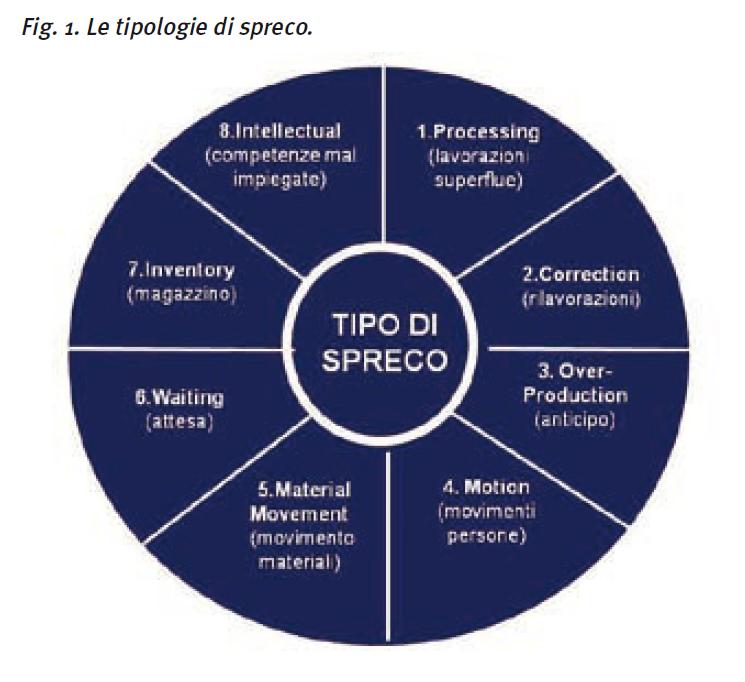
- Ricollocazione di documenti negli archivi (per es., l’incapacità di gestire al meglio gli archivi si traduce in attività straordinaria di ‘pulizia’).
- Da un modello operativo ‘tradizionale’, in cui la Front Line raccoglie le esigenze del cliente per poi passarle a strutture specializzate di Back Office, che le trattano in maniera asincrona rispetto alla domanda;
- A usufruire della prestazione in momenti non di picco;
Pagina
articolo, Attilio Ragusa, clienti, cost saving, costi, lean, lean product development, lean thinking, organizzazione, processo, Produzione, Roberto Bugatti, sistema produttivo, valore