Il valore del ‘gemello digitale’ per le aziende manifatturiere
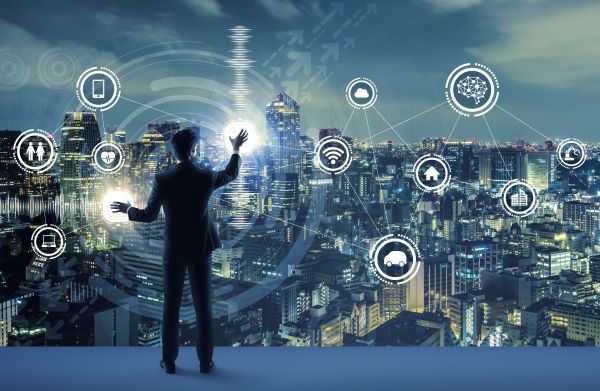
Nell’ambito dell’Industria 4.0 si possono fornire diverse definizioni di ‘gemello digitale’. Siemens PLM Software, business unit della divisione Digital Factory di Siemens, con l’espressione digital twin intende un insieme di modelli che forniscono informazioni utili per progettare, validare e ottimizzare un prodotto, un processo o un impianto produttivo in ambito virtuale.
Grazie al gemello digitale è possibile svolgere queste operazioni in modo veloce, preciso e con la massima fedeltà rispetto all’oggetto vero e proprio, quindi alla sua controparte fisica: i digital twin sfruttano infatti dati raccolti dai sensori installati su oggetti fisici per rappresentare il loro stato, le condizioni di funzionamento o la posizione in tempo quasi reale.
Siemens PLM Software, da oltre 25 anni sviluppa soluzioni software per la robotica avanzata e dal 2007 ha consolidato la sua leadership nella simulazione di prodotti e processi digitali attraverso importanti acquisizioni e investimenti in M&A.
L’azienda ha voluto condividere la propria esperienza nel corso della prima visita in Italia di Jan Leuridan, Senior Vice President, Simulation and Test Solutions di Siemens PLM Software, e CEO di Siemens Industry Software Belgio.
Un processo in tre fasi
“Oggi è possibile realizzare gemelli digitali per la progettazione di prodotti, la pianificazione di processi manifatturieri e la produzione attraverso il ciclo della Smart factory e lo Smart product”, ha spiegato Leuridan, il quale ha illustrato attraverso diversi esempi l’utilizzo classico di un gemello digitale, che si articola in tre fasi principali: progettazione di prodotto, pianificazione del processo manifatturiero, cicli di feedback.
Nella prima fase è possibile ottenere un modello computerizzato completo del prodotto, che consente la convalida e il collaudo virtuale praticamente al 100%. In questo modo si elimina il ricorso a prototipi, si riducono i tempi di sviluppo, si migliora la qualità del prodotto finale e si velocizzano le interazioni sulla base dei riscontri dei clienti.
La seconda fase offre la possibilità unica di simulare, validare e ottimizzare virtualmente l’intero impianto di produzione. Consente quindi di verificare come verrà costruito il prodotto, con tutti i suoi componenti principali e sottoassiemi, utilizzando i processi, le linee e l’automazione di produzione previsti.
All’interno del gemello digitale si possono integrare anche gli aspetti logistici. Ciò può aiutare i team di pianificazione a progettare una soluzione logistica efficace per alimentare le linee di produzione.
La terza fase permette invece di raccogliere le informazioni e inviare i dati più significativi al reparto di sviluppo prodotto che si occupa della pianificazione della produzione o dell’impianto, per analizzare i risultati ottenuti e migliorare i prodotti futuri.
Dal modello virtuale a quello reale
Il passaggio è quello da un iniziale prodotto virtuale a una produzione ancora virtuale, per arrivare a una produzione reale e quindi al prodotto reale.
“Questo è ciò che chiamiamo Generative Engineering: dalle necessità si effettua una simulazione, analizzando i dati e sincronizzando i processi, per arrivare al prodotto finito”, ha affermato Leuridan, sottolineando l’importanza di puntare sui test oltre che sulle simulazioni
Il grande valore del gemello digitale è quello di offrire flessibilità in produzione per ridurre i tempi necessari per progettare un prodotto, per pianificare un processo e un impianto produttivo e per progettare un impianto di produzione.
“Il gemello digitale migliora la qualità e supporta nuovi modelli di business che offrono alle piccole e medie imprese la possibilità di ampliare le loro officine e dotarle di più funzionalità high tech”. Ciò consente alle aziende di “diventare più flessibili, ridurre il time to market e i costi, migliorare la qualità e aumentare la produttività a tutti i livelli dell’organizzazione”.
L’Internet of Things (IoT), la Virtual Reality e il cloud possono servire in questo ambito non solo in ottica predittiva, ma anche per dare feedback nel corso del processo produttivo. “Si può dire che l’IoT sia il Rinascimento del Testing”, ha concluso Leuridan.