I gemelli digitali diventano realtà
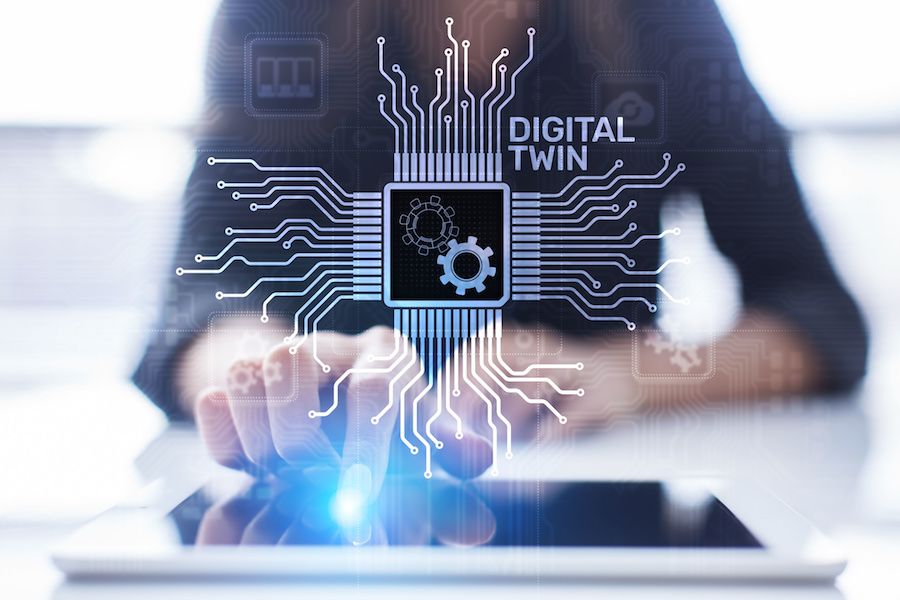
Nell’impiantistica i tempi di sviluppo e la progettazione sono oggi processi sequenziali, mentre il prototipo reale richiede un lavoro dispendioso sia in termini di tempo sia di costi. Prima della messa in servizio sono necessari numerosi cicli di correzione e spesso è necessario un certo intuito per stabilire il nesso tra errori e componenti. Un gemello digitale può essere d’aiuto, ma senza un gemello digitale delle informazioni nel processo mancano dati di prodotto e informazioni importanti.
Oggi nell’impiantistica i gemelli digitali offrono come modelli 3D un valido supporto per la realizzazione di simulazioni e test. In genere, con ciò s’intende un sistema cyberfisico che fornisce informazioni dettagliate per le analisi. Queste informazioni si riferiscono tuttavia solo al ‘qui e ora’. Un produttore di impianti vuole però sapere anche quali documenti e informazioni sono stati creati nel corso del progetto.
Se l’utilizzo di gemelli digitali include anche il funzionamento, saranno generate localmente una quantità di informazioni relative alla struttura dell’impianto della macchina specifica. Tali informazioni sono registrate in un cosiddetto gemello digitale delle informazioni, più o meno la memoria a lungo termine dell’impianto. I sistemi di Product Lifecycle Management (PLM) sono i più adatti per creare il dossier del ciclo di vita.
Nel corso del tempo, in essi nasce il gemello digitale delle informazioni dell’impianto, essenziale per la realizzazione del gemello digitale stesso. Ed è proprio nel caso dei sistemi cyberfisici, cioè dei sistemi con un’elevata percentuale di software e interconnessione, che diventa sempre più importante il binomio tra il gemello digitale e il gemello digitale delle informazioni. Grazie a essi è possibile stabilire nuovi modelli di business (offerte di servizi).
La costruzione dell’impianto è suddivisa in tre fasi consecutive fondamentali: acquisizione, sviluppo (progettazione personalizzata dell’impianto) e funzionamento dell’impianto (utilizzo per lo scopo previsto per tutto il suo ciclo di vita). I gemelli digitali, come repliche virtuali di un impianto, vengono utilizzati in ogni fase del suo ciclo di vita.
Durante lo sviluppo, tutte le funzioni successive, incluse quelle dei controllori logici programmabili (PLC), possono essere simulate sul gemello così come avviene in un controllo reale. Durante la messa in servizio e la successiva produzione, il gemello viene azionato utilizzando i dati macchina aggiornati e quelli dell’impianto reale per poter simulare su di esso il comportamento del sistema.
I compiti di un gemello digitale sono quindi diversi, a seconda della fase in cui viene utilizzato. Come modello virtuale dell’impianto, il gemello digitale riproduce le condizioni attuali dell’impianto attingendo a strutture, documenti e modelli del gemello digitale dell’informazione.
Impianti reali nel sistema PLM
Un tale concetto di gemello digitale e gemello digitale delle informazioni è stato sviluppato negli ultimi due anni nel progetto di ricerca Industria 4.0 CPPSprocessAssist realizzato presso l’Istituto Fraunhofer di Magdeburgo per la gestione e l’automazione delle fabbriche IFF. Il gemello digitale delle informazioni è stato riprodotto da PRO.FILE di PROCAD. Il progetto, che ha ottenuto un finanziamento di circa 2 milioni di euro, ha come obiettivo di dimostrare in termini concreti e reali come l’interazione tra il gemello digitale e il gemello digitale delle informazioni possa aumentare la disponibilità dell’impianto in funzione. A tale scopo, sono stati sviluppati un sistema di assistenza basato su sistemi di produzione cyberfisici, composto da moduli di conformità dei processi e sensori, e un sistema di gestione delle informazioni parallelo basato su PRO.FILE.Per scaricare l’articolo “Digital Engineering con PRO.FILE“, CLICCA QUI
ll sistema PLM come gemello digitale delle informazioni supporta il gemello digitale. Esso fornisce tutte le informazioni: dallo sviluppo alla pianificazione del progetto fino alla messa in servizio e documenta in fase operativa tutte le tappe di costruzione dell’impianto. Un ruolo speciale in questo contesto spetta all’identificativo apparecchiatura (BMK), un numero di componente specifico (ID) di ogni singolo pezzo dell’impianto, per esempio di un motore installato da un determinato cliente. Il BMK consente un accesso chiaro a parti e documenti. Quando si costruisce un gemello digitale esso deve essere assegnato il più presto possibile in modo da accelerare i processi successivi e mettere tempestivamente in parallelo le varie discipline M-CAD, E-CAD e il programma di controllo. Nel software PLM, il progettista può assegnare il BMK; in questo modo in esso è riprodotto non solo l’impianto sviluppato ma anche quello reale. Sulla struttura degli impianti-Bill of Material (BOM) nel Backbone Product Data di PLM sono memorizzati a livello centrale tutti i dati, i documenti e le informazioni sull’impianto disponibili su richiesta. Il BMK è memorizzato direttamente nell’archivio delle parti. La documentazione è pertanto conforme alla norma DIN EN 77005 (dossier del ciclo di vita) e può essere completata durante la messa in servizio e l’esercizio. Oggi nell’impiantistica i tempi di sviluppo e la pianificazione del progetto sono per lo più processi sequenziali e richiedono un’intensa comunicazione e coordinamento tra i singoli reparti. Il progettista consegna il suo lavoro ‘inanimato’ all’ingegnere dell’automazione il quale ha poi il compito di fargli prendere vita cercando di entrare nella mente del costruttore. L’impianto viene costruito fisicamente come prototipo di dimensioni reali per testare funzioni e cinematica. Non di rado c’è poi un brusco risveglio quando si scopre che qualcosa non funziona come previsto per una mancanza di coordinamento.Il codice di controllo è generato già nel tool di creazione delle cinematiche
Per questo motivo, il progetto di ricerca ha utilizzato uno strumento di cinematica messo a punto in proprio e chiamato VINCENT (Virtual Numeric Control Environment). Esso si basa sul sistema PLM dal quale carica modelli CAD 3D attraverso il formato di scambio STEP e consente la dimostrazione virtuale dei processi movimentando gli elementi dell’impianto da CAD in base a tempo, posizione, velocità e accelerazione. I componenti vengono riuniti in assiemi e gruppi di modelli cinematici e le componenti CAD sono assegnate a strutture cinematiche (corpi, assi, connessioni). VINCENT provvede inoltre all’ottimizzazione del modello (gestione dei casi di simulazione) e integra il gemello con elementi aggiuntivi quali sistemi di utensili, sensori e telecamere. I moduli dell’impianto esistenti vengono modificati in modo permanente, cosa che deve essere documentata. Se la geometria viene modificata nel sistema CAD, questa modifica viene trasferita a VINCENT tramite un file STEP. La cinematizzazione controlla se i cambiamenti sono fattibili e se i nuovi processi sono possibili senza causare collisioni. I risultati della simulazione (protocolli, documentazione, BMK) vengono restituiti dal gemello digitale al gemello delle informazioni. La modifica viene quindi documentata a ritroso, senza averla eseguita realmente. Una modifica del controllo viene simulata nel gemello digitale con VINCENT che carica i dati CAD dal sistema PLM. Dopo che questi risultati di simulazione sono stati trasmessi, il nuovo software di controllo viene trasferito alla produzione o all’impianto stesso.Tempi di messa in servizio ridotti fino al 70%
La cinematizzazione è fondamentale nell’interazione tra progettazione e programmazione del controllo che sono tradizionalmente autosufficienti. Caricando la struttura inanimata nello strumento cinematico, l’impianto viene messo in movimento soltanto virtualmente. Il progettista può simulare il funzionamento, mostrarlo al cliente e creare le basi per l’ingegnere dell’automazione. Il codice di controllo può essere generato direttamente nello strumento di cinematizzazione, il che fa risparmiare all’ingegnere dell’automazione una buona parte del suo faticoso lavoro. In questo modo si riducono le incomprensioni e si riesce a generare e fornire un codice sicuro. L’istituto Fraunhofer IFF ha testato il sistema presso vari costruttori di macchine speciali in condizioni di esercizio effettive, 24 ore su 24, 7 giorni su 7, riscontrando una riduzione fino al 70% dei tempi di messa in servizio e fino al 50% dei tempi di sviluppo e programmazione. Per riuscire ad accompagnare i processi di cambiamento in azienda senza dover ricominciare ogni volta da capo, è necessaria una gestione delle attività. Con il prodotto PRO.CEED, PROCAD fornisce un modulo adeguato in grado di supportare i processi di lavoro attraverso il controllo delle attività e dei processi. Per quanto riguarda le fasi nella costruzione degli impianti, VINCENT inizia dalla progettazione tardiva degli impianti. Quando si parla di elaborazione di un progetto preliminare virtuale s’intende che i requisiti non vengono fissati in un testo, ma si passa direttamente alla simulazione. Ulteriori campi di applicazione per gemelli digitali del tipo descritto sono l’ingegneria interdisciplinare (migliore cooperazione tra meccanica, elettronica, elettronica e software), il supporto all’assemblaggio, la messa in servizio e l’assistenza operativa.Step fondamentale per l’Industria 4.0
Un gemello digitale cinematizzato con l’aiuto di dati storici del gemello digitale delle informazioni fornisce una replica virtuale dell’impianto e consente di simulare tutte le funzioni successive. Le modifiche alla geometria dell’impianto possono essere elaborate completamente in modo digitale, inclusa una visualizzazione cinematica del gemello digitale con generazione automatica del codice di controllo. Le modifiche alla produzione vengono distribuite automaticamente e rinviate al gemello digitale delle informazioni. Questo concetto, concepito nel progetto di ricerca del Ministero Federale dell’Istruzione e della Ricerca, ha creato una base tecnica in grado di offrire un’assistenza veloce e pianificabile che diventa una componente importante di Industria 4.0. Concetto e utilizzo del gemello digitale delle informazioni diventano realmente comprensibili e possono essere utilizzati sin da ora.Per scaricare l’articolo “Digital Engineering con PRO.FILE“, CLICCA QUI
gemello digitale, industria 4.0, Pro.File PLM, Product Lifecycle Management, VINCENT