Efficienza energetica: tecnologie, personale e ‘best practice’
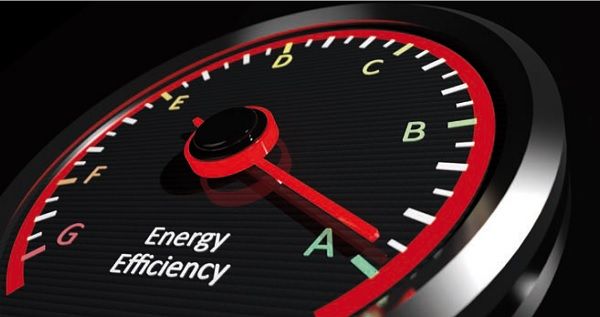
Efficienza energetica: tecnologie, personale e ‘best practice’
In un articolo precedente “Le fabbriche del futuro verso l’eco-economia”, Sistemi&Impresa, settembre 2014, abbiamo trattato la visione delle eco-factory e la necessità di passare dall’energy management all’energy efficiency management: in questo numero trattiamo più in dettaglio i fondamenti di un sistema di management dell’Energy Efficiency, cioè un ENergy Efficiency Management System (ENEMS).
di Claudio Palasciano
In un mondo in cui le risorse (energia, acqua, minerali, cibo), stanno diventando sempre più scarse, e il settore industriale è il responsabile di un terzo del consumo energetico mondiale e di quasi il 40% delle emissioni globali di biossido di carbonio, l’efficienza energetica e, in generale, nell’uso delle risorse utilizzate dai sistemi produttivi stanno diventando un fattore critico per la competitività, sia per gli aspetti legati alla sostenibilità ambientale sia quelli di riduzione di costo, insieme alla crescente sensibilità dei consumatori verso i prodotti verdi e sostenibili.
Per implementare l’efficienza energetica si devono integrare aspetti tecnologici e socio-tecnici, con un approccio formale di management: un ENergy Efficiency Management System (ENEMS) basato su una visione della fabbrica come sistema complesso. Adottare una visione sistemica significa focalizzare l’attenzione non solo sugli aspetti di conduzione degli impianti, ma anche sul ciclo di vita e in particolare il design degli impianti stessi, tenendo conto della complessa rete di interconnessioni fisiche e informative tra i vari sistemi di fabbrica e dei diversi comportamenti e prospettive del personale e dei manager coinvolti.
Da un lato, la gestione del consumo energetico e dei relativi costi porta all’eliminazione degli sprechi e a risparmi cumulati nel tempo. Dall’altro, è dimostrato che i costi energetici sono una parte rilevante del total cost of ownership (TCO) di un’installazione, quindi è importante pensareal ciclo di vita delle fabbriche nel suo complesso, adottando metodi di Energy Efficient Design (EED) in termini di integrazione, dato che, spesso, non è detto che diversi e separati interventi di ottimizzazione locale portino all’ottimizzazione globale. Vediamo nel seguito quali sono gli elementi fondamentali di cui tenere conto per progettare e gestire un ENEMS: tecnologie, personale, best practice.
Le tecnologie
Come visto nel precedente articolo Le fabbriche del futuro verso l’eco-economia (Sistemi&Impresa, settembre 2014), sta aumentando la disponibilità di Best Available Technologies (BAT) per l’efficientamento energetico, dal livello di componente, macchina o work center fino a quello di building e fabbrica.
Dal punto di vista del ciclo di vita delle fabbriche, i sistemi nuovi possono essere ottimizzati in termini di efficienza energetica durante la fase di design oltre che durante le Operations, attraverso costante manutenzione e monitoraggio.
È particolarmente importante adottare un approccio integrato di EED, dato che, anche se si possono adottare BAT disponibili a vari livelli, è solo la visione completa a livello di fabbrica che può portare ai risultati di efficientamento migliori. Ad esempio, le sperimentazioni di Siemens AG (www.emc2-factory.eu) mostrano che una tecnolo-gia di processo nuova come la saldatura ad attrito (Friction Stir Welding – FSW) potrebbe risultare, in un’analisi centrata sugli aspetti energetici puri di processo, come assolutamente comparabile alle classiche saldature MIG/MAG in termine di costi operativi: la FSW risulta invece preferibile in una visione sistemica in cui si tenga conto del rilevante consumo energetico del sistema di ventilazione in presenza di gas di saldatura.
Tracciamo qui alcuni cenni alle attività specifiche di EED di una nuova fabbrica, che possiamo inserire nelle fasi ‘classiche’ di design della fabbrica: design concettuale di massima, design di dettaglio, processo di offerta, costruzione e deployment, operations.
Nella fase di design concettuale da un lato, si tratta ad esempio di identificare i fabbisogni energetici e i relativi costi lungo il ciclo di vita dei vari sottosistemi, e i principali parametri di design che influenzano il consumo energetico, coinvolgendo in un approccio collaborativo le persone/funzioni chiave che influenzano il consumo energetico stesso. Nella fase di design dettagliato, dall’altro, è possibile introdurre ottiche di ottimizzazione globale dei consumi energetici, considerando anche aspetti quali i sistemi di misura e controllo, le opportunità di recupero energetico, cogenerazione, la riduzione degli sprechi nei sistemi ausiliari (aria compressa, illuminazione ecc.). Diventa in questo contesto molto utile curare la richiesta di specifiche informazioni relative all’efficienza energetica nei documenti di offerta relativi alle macchine e agli impianti ausiliari acquisiti.
L’esperienza insegna che in genere le migliori efficienze si ottengono nei casi di nuovo design (il cosiddetto greenfield), ma non è detto che l’EED non si possa applicare anche in caso di retrofit o update di una certa rilevanza, magari coinvolgendo da subito esperti di efficienza energetica o l’energy manager.
Personale
Dal punto di vista delle risorse umane, il focus deve essere il mantenimento e lo sviluppo dell’expertise sull’efficienza energetica: attualmente, soprattutto nella gran parte delle imprese, il personale copre un ampio raggio di task relativi a varie macchine e/o impianti per cui vi è poca disponibilità di personale per task non routinari, come energy audit e monitoraggio dei consumi.
È quindi importante reclutare staff competente in efficienza energetica a supporto del personale operativo e/o utilizzare le attività di training per integrare l’efficienza energetica nella cultura organizzativa, accompagnando il training con azioni di comunicazione e di coinvolgimento del personale stesso, nell’ambito di un solido e continuativosupporto del top management, in termini di risorse umane e finanziarie insieme.
Il training necessario può essere basato su formazione in aula per mezzo di esperti o su autoapprendimento: anche se non vi è attualmente molto materiale di e-learning nell’area, è disponibile su internet molto materiale informativo sviluppato da organizzazioni dell’area anglosassone (si veda ad esempio il joint programme DOA e EPA), dell’unione Europea (e.g. EUREM) e nazionale (e.g. ENEA): si veda per dettagli ulteriori l’elenco dei riferimenti fornito con questo articolo. Un esempio interessante è quello del citato progetto europeo EUREM, che, fornendo 140 ore di lezioni in aula e circa 60 ore di autoapprendimento, ha consentito in media a ogni partecipante di ottenere risparmi energetici quantificabili in circa 30 volte i costi diretti del corso (intorno ai 2.000 euro).
Best practices
Quanto visto finora ci consente di definire la struttura base del ciclo ENEMS, basato su un forte commitment del top management, in un processo iterativo del tipo Plan/Do/Check/Act:
a) definizione delle policy aziendali di efficienza energetica con un approccio sistemico;
b) pianificazione delle attività, attraverso la definizione di obiettivi e target relativi;
c) design e conduzione delle procedure organizzative, incluso training, approcci collaborativi e comunicazione interna;
d) monitoraggio e benchmarking;
e) preparazione di rapporti regolari con eventuale validazione esterna (certificatore o consultant);
f) analisi della configurazione tecnologica, incluse considerazioni di investimento e/o dismissioni di impianti/tecnologie, in ottica possibilmente di integrazione EED.
Esperienze aziendali
Aziende di primaria importanza, anche a livello internazionale, puntano sull’efficienza energetica, spesso con l’adozione integrata di tecnologie, di sistemi e procedure per una gestione formalizzata dell’Energy Efficiency Management.
Un esempio dell’attenzione crescente delle imprese verso l’efficienza energetica viene dai risultati di una recente indagine promossa dal comitato scientifico di FabbricaFuturo e condotto da ESTE in collaborazione con OD&M consulting: circa il 10% delle imprese interpellate pensa che le tecnologie di efficientamento energetico siano le più importanti nei propri piani di investimento.
Le aziende dei settori energy-intensive hanno una lunga esperienza di efficientamento energetico: ora anche aziende di produzione di altri settori e dei servizi puntano con risultati ritenuti positivi su piani di continuous improvement nel campo dell’efficienza energetica.
Il gruppo Whirlpool, leader nella produzione di elettrodomestici, ad esempio, è impegnato in impegnativi progetti di ricerca, in particolare con la sua divisione di ricerca che ha acquisito expertise in vari settori, fra i quali anche la trasmissione di energia e l’efficienza energetica.
Siemens AG, nell’ambito delle sue attività di ricerca e innovazione, ha sviluppato recentemente un pilot volto all’efficientamento anche energetico della fabbrica di Vienna dove vengono prodotte carrozze metro e ferroviarie. In tale contesto, tra i molti studi condotti e le varie tecnologie implementate nell’ambito del progetto (per dettagli si veda www.emc2-factory.eu/downloads), oltre all’esempio citato nei paragrafi precedenti riguardo alle tecnologie di processo, a livello macchina, Siemens ha sperimentato un modulo sviluppato da uno dei partner del progetto (Festo AG) per il monitoraggio e la riduzione automatica delle perdite di aria compressa, oltre a un sistema di programmazione della produzione e di scheduling multi-obiettivo, in grado anche di tenere conto di picchi di carico energetico.
Lufthansa Technik (Lufthansa Group) è un leading provider mondiale indipendente di manutenzione/ repair per l’aviazione civile. L’acquisizione della direttiva europea EU 2020 e dei relativi target ha portato la compagnia a implementare un ENEMS basato su identificazione dei target e delle policy di efficienza energetica, un solido sistema di misurazione e reporting, dapprima basato su audit e poi su un sistema informativo specializzato, cheha portato l’azienda a rilevanti risparmi in termini di consumo energetico. L’azienda ha accompagnato gli interventi con una vera e propria campagna di marketing/comunicazione interna per promuovere a tutti livelli l’efficienza energetica fra il personale, coinvolgendolo anche in raccolte di idee e condivisione di best practice, per facilitarne la diffusione e l’adozione nelle varie locazioni produttive dell’azienda.
Alcuni riferimenti
– EMC2-Factory project, Solutions for experts and decision makers, www.emc2-factory.eu
– ENEA, Rapporto Annuale Efficienza Energetica RAEE, 2015, www.enea.it/it/pubblicazioni/pdfvolumi/ raee-2015.pdf
– Environmental Protection Agency (EPA), www.energystar.gov
– EUREM European Energy Manager, www.ihk-eforen.de/display/eurem/EUREMplus
– European Commission Reference Document on Best Available Techniques for Energy efficiency, February 2009, http://eippcb.jrc.ec.europa.eu/ reference/BREF/ENE_Adopted_02-2009.pdf
– McKinsey report, Resource Revolution, Meeting the World’s energy, materials, food and water needs, 2011
– Palasciano, C., Le fabbriche del futuro verso l’ecoeconomia, dall’energy management all’energy efficiency management, Sistemi&Impresa, settembre 2014
– PEW Center, www.c2es.org/energy-efficiency
– Prindle, W.R. Solutions: from shop floor to top floor, best business practices in energy efficiency, ICF, 2009.

best practices, Claudio Palasciano, eco-nomia, efficienza energetica, EMC2-Factory project, enea, EPA, EUREM, Lufthansa Technik, mckinsey, personale, PEW Center, Prindle, Siemens AG, tecnologie, Whirlpool