Le Fabbriche del Futuro verso l’eco-economia: dall’energy management all’energy efficiency management

di Claudio Palasciano, Politecnico di Milano – Dipartimento di Ingegneria Gestionale, Manufacturing Group
1. Il contesto competitivo
Con il mercato globale in costante trasformazione, spinto della crescita economica e della popolazione mondiale, le aziende europee e italiane in particolare devono affrontare una dura competizione a causa della globalizzazione e della pressione sulle risorse aziendali, dai costi del lavoro a quelli dell’energia e delle commodities, dell’aumento, a livello mondiale, del rischio su risorse importanti, dall’acqua alle materie prime per l’elettronica.La strategia EU2020 della
commissione europea mira a un’economia ‘knowledge and innovation-based’, che promuove l’efficienza nell’uso delle risorse, l’attenzione all’ambiente e alla competitività allo stesso tempo. Questa eco-economia attenta gli impatti ambientali e allo stesso tempo a livelli alti di occupazione e che porta coerenza sociale e territoriale può essere abilitata solo da un settore manifatturiero in grado di sviluppare e fornire prodotti innovativi e sostenibili mediante sistemi produttivi smart ed eco-friendly. La sostenibilità è dunque divenuta un key topic nell’agenda di politici e managers.
Un recente rapporto McKinsey riporta come effetti positivi sul ritorno degli investimenti possano derivare da politiche di vendita che facciano leva sull’efficienza nell’uso delle risorse, da value proposition che includano bassi impatti ambientali e dalla riduzione di costi operativi attraverso il miglioramento dell’efficienza nella gestione di tutte le risorse produttive (energia, scarti, acqua, sostanze dannose etc.). A ciò si aggiunge i’impatto positivo sul brand dell’immagine ‘green’ sulle politiche di vendita e mediante “signaling” verso investitori e stake-holders istituzionali.
Quindi, oggi essere ‘green’ conviene economicamente, ecologicamente e dal punto di vista della riduzione del rischio di approvvigionamento delle risorse di produzione. In una parola, anche i manager si rendono conto del vantaggio competitivo di poter contare su fabbriche ’green’. In questo contesto il settore manifatturiero europeo deve cambiare il suo approccio alla competizione. Le fabbriche e le supply chains devono essere ‘ritarate’ per fare i conti con la loro crescente complessità interna, e allo stesso tempo, reagire alle pressioni sui costi garantendo una performance multidimensionale che ormai comprende obiettivi spesso in trade-off, quali livello di servizio, qualità, flessibilità produttiva interna e alto livello di personalizzazione dei prodotti. Tutto ciò minimizzando gli impatti ambientali. La Fabbrica del Futuro ha bisogno di una trasformazione verso sistemi produttivi “energy and resource aware” e a bassa carbon footprint: questi nuovi sistemi saranno progettati e gestiti come un tutto, un sistema integrato, in cui ogni parte ha il suo obiettivo e sistema di gestione specifico, ma la visione e performance complessiva va vista in senso ‘sistemico’. In questo contesto l’efficienza energetica nel settore manifatturiero è naturalmente il primo obiettivo da raggiungere: la riduzione dei consumi e degli sprechi energetici ha il doppio effetto di ridurre i costi operativi e la carbon footprint e spesso gli interventi di efficientamento energetico hanno l’effetto collaterale di risparmiare altri “waste”, ad esempio nell’uso dei materiali di consumo (liquido lubro-refrigerante, consumo dei tools). Per progettare e gestire le future fabbriche servono nuove metodologie, sistemi e strumenti software:
in questo senso, lo sforzo d’innovazione e sviluppo è ben rappresentato, a livello internazionale, dalla ricerca sul manufacturing del progetto Intelligent Manufacturing Systems (www.ims.org) e, a livello europeo, dal numero di progetti di ricerca raccolti nel portale dell’innovazione dell’ European Factory of the Future Research Association (EFFRA): www.effra.eu.
2. L’efficienza energetica nel contesto nazionale
Il contesto italiano presenta ancora maggiori criticità riguardo al consumo dell’energia, per tre motivi: la forte dipendenza dai combustibili fossili e il conseguente alto impatto in termini di carbon footprint, a cui si aggiunge il problema della sicurezza dell’approvvigionamento, in quanto l’Italia dipende dall’estero per l’85% del fabbisogno.
In questo scenario le factory of the future Italiane vedono quindi come priorità l’efficientamento della risorsa energy. Secondo uno studio di ENEL del 2013, sul periodo 2013-2020 il risparmio potenziale con l’adozione sistematica delle Best
Available Technologies (BAT) di efficienza energetica a livello industriale e residenziale viaggia tra i 195 e i 288 TWh annui, a seconda dello scenario economico prevedibile, rispettivamente di sviluppo moderato o ottimo.
Nonostante lo sviluppo di strategie e politiche prescrittive per l’efficienza energetica da parte dell’Unione Europea (gli obiettivi EU2020 di riduzione del 20% dei consumi energetici, che si sono riflessi a livello nazionale nel Piano di Azione per l’Efficienza Energetica (PAEE 2007 con revisione nel 2011), molte delle tecnologie di efficienza energetica non hanno ancora raggiunto un livello di diffusione sufficiente per creare effetto massa critica e/o hanno tempi di ritorno dell’investimento non velocissimi, per cui una politica di incentivazione pubblica diventa importante: purtroppo dobbiamo constatare una certa lentezza delle politiche energetiche nel reagire in questo senso, come anche vedremo nel seguito.
3. I driver abilitanti l’efficienza energetica
Cosa serve sapere per muoversi nel campo dell’efficienza energetica? I principali driver abilitanti l’efficienza energetica sono:
• La disponibilità e utilizzo delle Best Available Technologies (BAT) di efficienza energetica.
• L’adozione dei più recenti standard e l’utilizzo delle normative e dei meccanismi di incentivazione in particolare.
• L’adozione di corretti comportamenti da parte del personale di stabilimento e del management in termini di strategie, piane e obiettivi di efficienza energetica.
Le aziende medio-grandi, con processi decisionali strutturati e già orientate alla ricerca di opportunità di miglioramento e di ottimizzazione, sono sicuramente pronte per questi nuovi sviluppi, anche se molte sono le barriere all’adozione e utilizzo efficace delle tecnologie di efficienza energetica: barriere culturali, organizzative, tecnologiche.
Un discorso a parte vale per le PMI per le quali alcune specifiche barriere all’adozione delle tecnologie e dei comportamenti per l’efficienza energetica sono particolarmente critiche e a volte impediscono l’adozione. In particolare, secondo diversi studi, le PMI soffrono soprattutto a causa dell’esistenza di diverse priorità aziendali che generano quindi messa a disposizione di risorse (sia umane sia finanziarie) di minore entità nel campo dell’efficienza energetica, indipendentemente dalle considerazioni economiche riguardo ai potenziali risparmi.
Nelle prossimi sezioni faremo una carrellata sui driver abilitanti, per molti dei quali non è detto che valga il paradosso che per fare risparmio in bolletta a volte occorrono rilevanti investimenti in tecnologie abilitanti, che per molte aziende sono un lusso di questi tempi.
3.1 Le BAT per il consumo energetico
Iniziano ad essere disponibili molte tecnologie ‘energy efficient’ ai vari livelli, da quello di tecnologia di processo/ macchina a quello di linea, su fino al sito produttivo nel suo complesso.
A livello di singola macchina e processo produttivo le aziende stanno sperimentando nuove tecnologie di processo:
• tecnologie di machining MQL (Minimum Quantity Lubricant) in grado di fare risparmiare sia energia che liquido di raffreddamento con un potenziale tempo di payback di massimo tre anni.
• Saldatura ad attrito FSW, che può essere utilizzata in particolare in campo aerospaziale in sostituzione del rivettaggio, alleggerendo le strutture.
• Machine utensili con controlli energy saving (start/stop, stand by mode), in grado di ridurre sostanzialmente il consumo energetico delle macchine attraverso controlli intelligenti che prevedono il tasso di arrivo delle parti da lavorare e/o raccolgono segnali da altre macchine guaste o in ritardo.
A livello di linee e reparti nuovi sviluppi sono prevedibili riguardo:
• Linee di assemblaggio e centri di lavoro con machine equipaggiate di sistemi di controllo ‘energy aware’ e robot alleggeriti.
• Sistemi di misura e monitoraggio multi-canale e multi sensore, atti a fornire le informazioni per i suddetti sistemi di controllo.
• Software per la simulazione di machine utensili e/o robot di processo, in grado di ottimizzarne le condizioni operative testando e valutando i relativi programmi di controllo.
• Interventi di efficientamento e progettazione ‘energy efficiency’ per i sistemi ad aria compressa: dal monitoraggio delle perdite d’aria all’utilizzo di sistemi di controllo automatico on/off dei compressori, in grado di adattare il set dei compressori attivi in base al carico di lavoro ottimizzandone l’efficienza.
A livello di sito produttivo e factory:
• Nuovi sistemi di misurazione e monitoraggio in real time della temperatura ambientale, in grado di alimentare sistemi automatici di controllo di riscaldamento e ventilazione.
• Software tools di virtualizzazione della fabbrica, in grado di simulare non solo le catene produttive ma anche i servizi generali (illuminazione, ventilazione e riscaldamento, ecc.) per ottimizzarne il design ma anche le condizioni di funzionamento.
• Adozione di sistemi di production planning e scheduling ‘energy aware’ in grado di generare in tempi ragionevoli piani di produzione e scheduling intelligenti, ad esempio in grado di evidenziare picchi di consumo elettrico con conseguente riduzione dei potenziali costi addizionali a causa di picchi di consumo fuori dalla fascia di consumo elettrico prevista.
3.2 Standard e normative
L’adozione delle tecnologie di efficienza energetica viene sicuramente fortemente favorita dallo sviluppo di standard condivisi tra gli utilizzatori e i produttori delle BAT di efficienza energetica. A livello di normative, la direttiva europea 2012/27/CE elabora prescrizioni in termini di auditing energetico, stimolo al mercato dei fornitori di BAT di ‘energy efficiency’, definizione di figure professionali dedicate alle tematiche energetiche in azienda. In Italia, la Strategia Energetica Nazionale (SEN) prevede quattro principali manovre per supportare l’efficientamento energetico del sistema Italia e delle fabbriche italiane:
1. rafforzamento delle normative e degli standard;
2. rafforzamento del meccanismo dei certificati bianchi;
3. introduzione di incentivi in conto termico;
4. prolungamento e revisione delle detrazioni fiscali.
Tra le forme di incentivazione troviamo, a fianco di quelle miste mirate al‘building’ quali conto termico e sgravi fiscali, alcune più dirette al settore industriale, quali i Titoli di Efficienza Energetica (TEE) e il Fondo Rotativo Kyoto. Queste ultime forme, di recente introduzione, non sono ancora valutabili: tuttavia sicuramente dovrebbero essere meglio supportati dalle politiche energetiche. Ad esempio, per i fondi rotativi c’è un certo ritardo nel fornire un’adeguata implementazione e dotazione finanziaria.
3.3 Comportamenti organizzativi
Il terzo driver di efficienza energetica consiste nell’adozione da parte del personale e del management di fabbrica delle corrette azioni di supporto agli interventi / progetti di efficienza energetica.
Secondo un survey svolto nel 2011-2012 su un campione di 85 aziende USA medio grandi, fra le quali IBM, Toyota, DOW Chemicals, l’entità e spesso anche il successo degli interventi di efficienza energetica dipendono dal supporto del management all’efficientamento energetico. L’efficienza energetica dunque non deve essere vista solo come un obiettivo dell’energy manager, ma soprattutto un obiettivo aziendale, con impatto sulla competitività aziendale stessa. Fra le best practices a livello organizzativo/ culturale possiamo trovare le seguenti.
1. Fare dell’efficienza energetica una strategia core dell’azienda, integrandola nelle strategie commerciali e nei sistemi decisionali del management.
2. Dare leadership e support organizzativo in modo da motivare/incentivare le azioni positive del personale operativo in particolare.
3. Dare obiettivi SMART (Specific Measurable, Accountable, Realistic and TImebound) di efficienza energetica, in modo da attivare corretti meccanismi di misura, reporting e tracking della performance di tutta la società.
4. Mostrare chiaramente e sostenere i risultati raggiunti dagli interventi e dalla strategia di efficientamento: le idee interessanti e con risultati di successo vengono riconosciute agli autori e correttamente premiate, anche con eventuali impegni delle risorse sostenuti nel tempo.
5. Supportare l’efficienza energetica nel lungo periodo, così da poter inoltre includere nei piani di efficientamento anche soluzioni meno sostenibili, quindi con tempi di ritorno dell’investimento anche di vari anni.
6. Comunicare e condividere i risultati degli interventi e dei piani di efficientamento energetico sia internamente sia esternamente, come parte integrante della strategia core di efficienza energetica. Importante diviene la progettazione e implementazione di piani di comunicazione volti alla creazione di ‘energy efficiency awareness’ sia all’interno sia all’esterno dell’azienda.
4. Conclusioni
Nel contesto della visione della fabbrica del futuro, congiuntamente progettata da industria e università, abbiamo visto che l’efficienza energetica nel manufacturing va di pari passo con le attuali esigenze di gestire la complessità, l’incertezza e il veloce mutamento che caratterizzano l’attuale contesto socio economico in cui vivono le nostre imprese di produzione, che possono ora non solo essere più efficienti, ma anche più competitive, attraverso value proposition ecologicamente e economicamente smart.
I driver abilitanti sono molti, dalle tecnologie e sistemi, alle normative e standard, fino alle best practices organizzative per la gestione dell’efficienza energetica. Per realizzare la visione della Fabbrica del Futuro, importanti centri di ricerca e università tecniche quali il Politecnico di Milano, l’Università degli Studi di Bergamo e la Technische Universität Braunschweig stanno lavorando in tutto il mondo, in stretta collaborazione con aziende industriali di primaria importanza, fra le quali COMAU, ABB, SIEMENS, nel contesto di progetti di ricerca anche finanziati dall’unione Europea. Tra questi progetti, con obiettivo specifico l’efficienza energetica e delle risorse, troviamo EMC2-Factory – Eco Manufactured transportation means from Clean and Competitive Factory (www.emc2-factory.eu) e PlantCockpit – Production Logistics and Sustainability Cockpit (www.plantcockpit.eu).
Nel nostro paese molte difficoltà e barriere costellano ancora il cammino verso questa visione, dalla lentezza delle reazioni dello Stato, alle barriere culturali, comunicative, finanziarie e organizzative che in particolare affliggono le nostre PMI.
Un altro elemento critico è il ritardo nello sviluppo in Italia di un sistema di politiche energetiche in grado di favorire l’adozione delle tecnologie ‘energy efficient’, nonostante i piani strategici e il rilevante impatto potenziale sia sui risparmi sia sulla carbon footprint. Si stima che il 40% circa dei citati risparmi sulla bolletta energetica nazionale possano derivare dall’adozione tecnologie con lunghi payback time e quindi poco ‘sostenibili’ nel breve: diviene quindi importante soprattutto il supporto dei meccanismi di incentivazione da attivare in tempi brevi all’interno delle politiche energetiche nazionali.
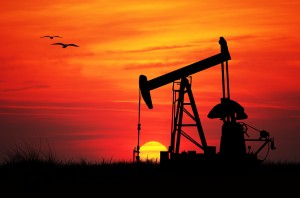
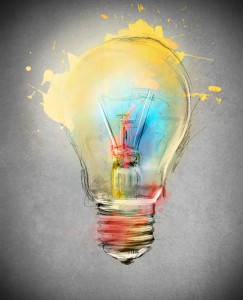
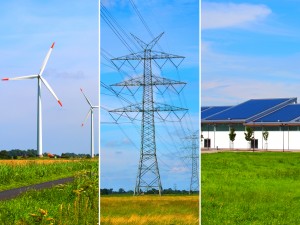

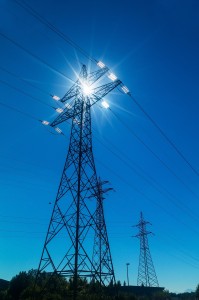
Best Available Technologies, Claudio Palasciano, energy management, Fabbriche del Futuro