Industria 5.0 e Metallurgia, il connubio della competitività
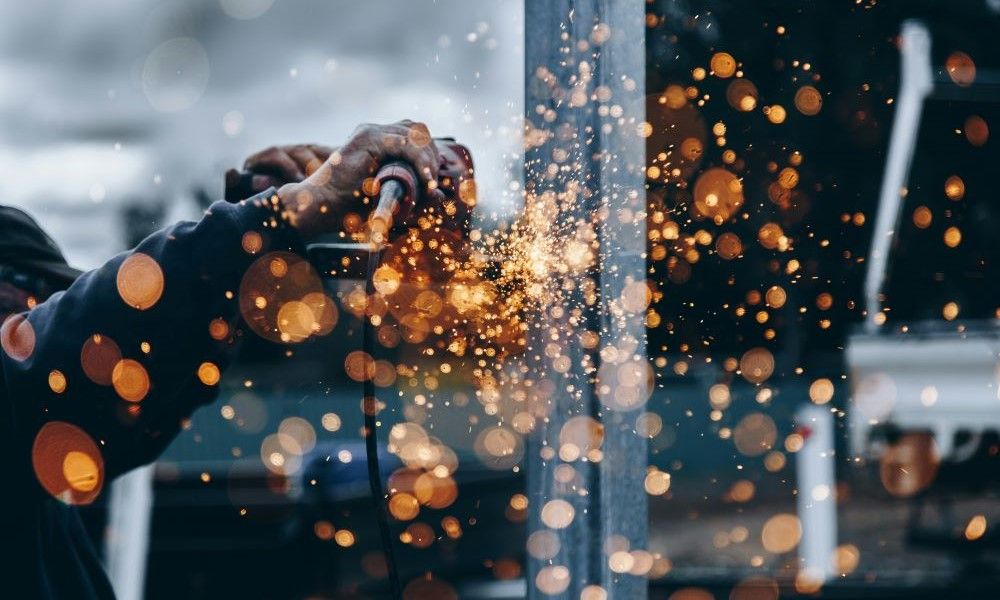
Il settore metallurgico è al centro di una trasformazione radicale. L’Industria 5.0 porta con sé una visione in cui tecnologie avanzate, sostenibilità e contributo umano si fondono, offrendo alle aziende nel comparto Metals – dalla lavorazione dell’acciaio alla fonderia di alluminio – gli strumenti per rispondere alle principali sfide di settore: gestione della domanda, riduzione dei costi energetici, minimizzazione degli sprechi e ottimizzazione della Supply chain. Questo è il punto di vista di Quin e Qgs, partner che supportano le aziende attraverso le proprie esperienze progettuali per affrontare le sfide del futuro.
Le aziende metals operano, infatti, in un contesto in cui flessibilità, rapidità di risposta e gestione ottimale delle risorse sono elementi centrali per mantenere la competitività. In questo mercato esigente, una Supply chain interconnessa e trasparente può rispondere con prontezza a una domanda volubile, rispettando al contempo standard di qualità elevati. La volatilità del mercato rende cruciale una previsione precisa e una gestione delle scorte che prevenga eccedenze e carenze.
Inoltre, le sfide logistiche e le oscillazioni di prezzo delle materie prime richiedono un approccio strategico agli approvvigionamenti, volto a contenere i costi senza compromettere la disponibilità dei materiali. Di pari passo, l’aumento dei costi energetici spinge le aziende a ottimizzare il consumo di energia, rispondendo così anche alle crescenti aspettative in termini di sostenibilità. Grazie all’Industria 5.0, le imprese possono, però, migliorare processi, affidabilità dei dati e qualità del lavoro, generando una sinergia che rafforza la capacità decisionale.
Integrazione tra ERP e MES al centro dell’Industria 5.0
Uno degli elementi centrali dell’Industria 5.0 è l’integrazione tra Enterprise Resource Planning (ERP) e automazione attraverso sistemi Manufacturing Execution System (MES). L’uso del MES permette alle aziende di monitorare e coordinare in tempo reale tutte le attività produttive, eliminando i colli di bottiglia e incrementando l’efficienza logistico-produttiva. Grazie a questa integrazione, le aziende metals possono ridurre i tempi di attesa e migliorare la precisione dei report, disponendo di dati aggiornati e accessibili in ogni fase del processo. In un ambiente interconnesso, le informazioni strategiche per il processo decisionale sono immediatamente disponibili, favorendo il coordinamento tra i reparti e aumentando la visibilità su tutta la catena del valore.
La gestione dei materiali, dalla ricezione fino al trattamento negli impianti, è fondamentale per le aziende metals. Con l’adozione di soluzioni avanzate di monitoraggio integrate al MES, ogni fase della lavorazione è seguita con precisione, minimizzando l’errore umano. La tracciabilità dei materiali assicura un controllo continuo, rilevando in tempo reale eventuali scostamenti dai parametri di processo, per garantire qualità e continuità produttiva. Grazie alla digitalizzazione e all’automazione, la gestione delle ricette e il controllo sui processi produttivi diventano più accurati, consentendo un utilizzo ottimale delle risorse.
Gestione degli scarti e digitalizzazione per l’ottimizzazione
Per contenere i costi e ridurre l’impatto ambientale, la gestione efficiente degli scarti è essenziale. L’adozione di sistemi MES avanzati e la revisione dei processi di pianificazione permettono di ottimizzare il flusso dei materiali in tutte le fasi produttive. Ciò migliora l’affidabilità dei dati e consente un monitoraggio più preciso delle risorse, creando un ciclo produttivo più sostenibile, con una gestione ottimizzata delle risorse materiali che riduce i costi della rilavorazione e degli sprechi.
La digitalizzazione nel settore metals va oltre, però, l’automazione dei processi produttivi, perché trasforma profondamente tutta l’organizzazione, incoraggiando una cultura aziendale orientata all’innovazione. Inoltre, l’introduzione di sistemi di Scrap Management consente di ottimizzare i costi della carica di rottame e ferroleghe, utilizzando algoritmi che sfruttano le caratteristiche dei materiali disponibili. Altri progetti di digitalizzazione, come il controllo di fucinati e fusi, la tracciabilità dei materiali e la gestione della logistica interna, migliorano la reattività dell’ambiente produttivo. L’utilizzo di app mobili per il monitoraggio in tempo reale dei macchinari e dei veicoli, inoltre, rende possibile una tracciabilità continua e aumenta l’efficienza nelle operazioni di magazzino e nelle aree logistiche.
Qualità e gestione documentale
Una pianificazione accurata e una gestione documentale efficiente sono fondamentali per garantire la conformità e la qualità del prodotto. L’uso di sistemi integrati che connettono ERP e MES permette alle aziende di raccogliere e analizzare dati in tempo reale, migliorando l’affidabilità nei processi di qualità. A questa si deve accompagnare una corretta gestione documentale, che riduce i tempi necessari per reperire le informazioni e assicura la conformità agli standard di settore. Con la possibilità di archiviare e accedere facilmente a documenti e dati in ogni fase, dalla pianificazione al controllo finale, le aziende possono rispondere rapidamente ai cambiamenti e alle nuove richieste di mercato.