Migliorare la gestione del magazzino con un sistema kanban ibrido
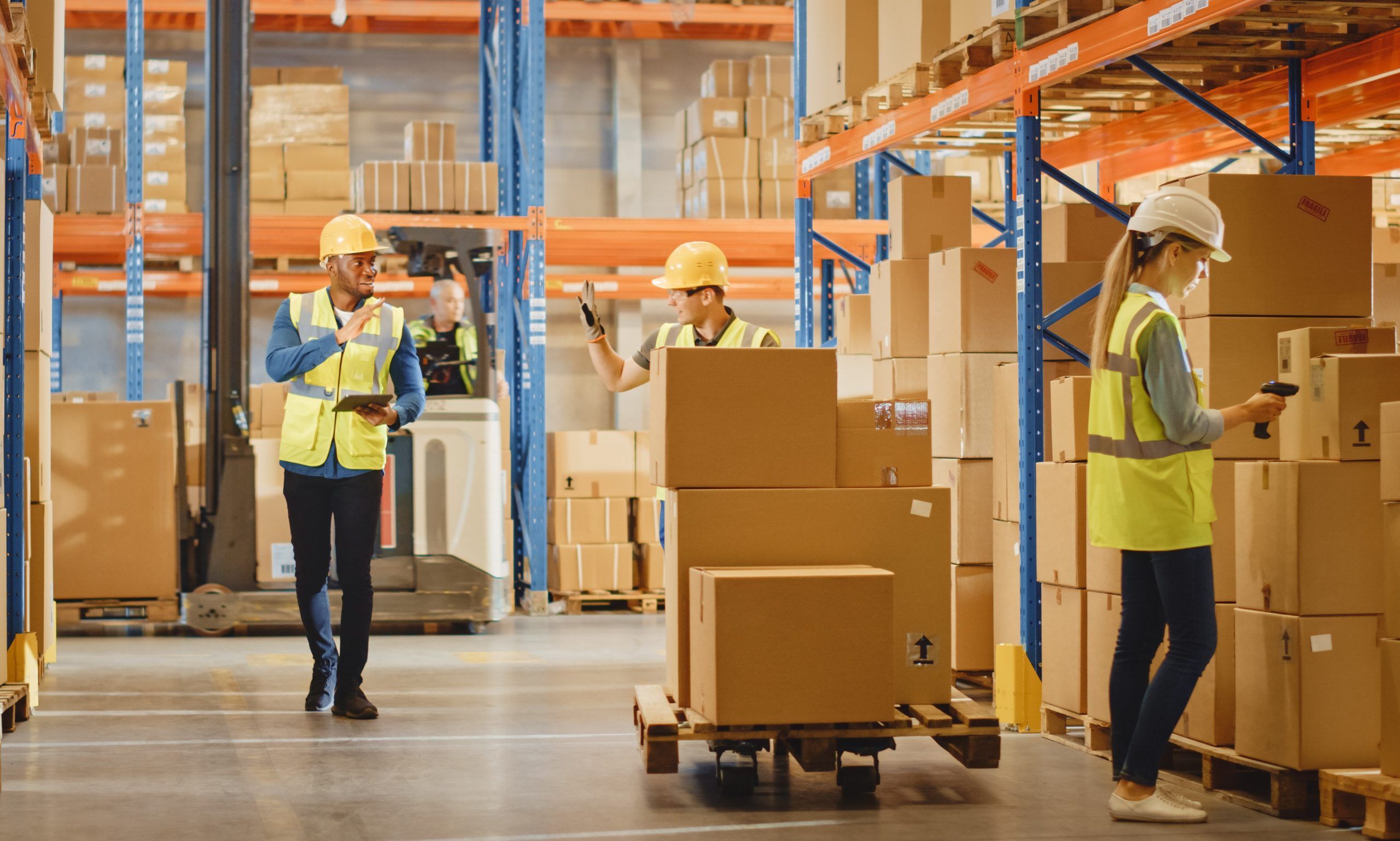
Accompagnare il radicale cambiamento che investe il settore manifatturiero, grazie alla diffusione delle tecnologie digitali e alla loro integrazione nella filiera produttiva, richiede l’impiego di soluzioni tecnologiche in grado di ottimizzare le Operations e supportare i processi di automazione industriale.
La gestione dei materiali è fra le attività che possono beneficiare significativamente della Digital transformation. Il suo obiettivo è duplice: garantire un adeguato livello di servizio, minimizzando l’insorgere di condizioni di criticità per i reparti produttivi; contenere i costi, evitando le giacenze non necessarie.
Tra le aziende che stanno usando le tecnologie digitali per innovare i processi c’è Master Italy, una media impresa del settore metalmeccanico con sede a Conversano (Bari), che progetta e realizza componentistica per serramenti in alluminio. L’implementazione delle tecnologie 4.0 ha determinato negli ultimi anni lo sviluppo di soluzioni sempre più complesse, con la progressiva trasformazione dei magazzini tradizionali in automatici.
In particolare, ci concentriamo sull’introduzione di un magazzino automatico che alimenta le varie celle di produzione. Ciò ha comportato la ridefinizione dei processi e delle politiche di gestione dei materiali. L’interesse discende dalla circostanza che sia stato studiato e implementato un sistema kanban non tradizionale, nel quale il ripristino dei contenitori in esso circolanti (di seguito “cassettine”) non avviene quando essi sono del tutto vuoti, bensì quando la quantità contenuta è inferiore a una soglia predeterminata (di seguito “soglia di ripristino”). Questa è la peculiarità che costituisce l’innovazione teorica proposta. La finalità di tale innovazione è adattare il sistema kanban alla gestione di un magazzino automatico, per il quale è rilevante perseguire la massima utilizzazione possibile dello spazio disponibile, caratterizzato da un costo superiore a quello di un magazzino convenzionale, quindi, limitando la presenza di cassettine parzialmente piene.
Il ruolo fondamentale dei magazzini nella logistica interna
Master Italy è nel mezzo di un percorso di digitalizzazione dei propri processi aziendali. Per quanto riguarda la logistica interna risulta fondamentale il ruolo dei magazzini, poiché la razionalizzazione delle operazioni di trasporto e stoccaggio ha ovvie implicazioni sul livello di servizio e sui costi. Lo studio del sistema è mostrato in Figura 1, in fase di progettazione e realizzazione, ed è composto dai diversi elementi: magazzino centrale, magazzino automatico, sistemi di carrelli a guida autonoma e sei celle di produzione. Il magazzino centrale è alimentato da codici inviati dai fornitori o dai reparti a monte: costituisce l’elemento iniziale del sistema considerato e alimenta il magazzino automatico a seguito dell’emissione di richieste di replenishment. Il magazzino automatico è, invece, destinato allo stoccaggio di componenti e semilavorati a servizio dei processi di produzione, dotato di un insieme di robot dedicati al caricamento degli Automated/Automatic guided vehicle (Agv). Il sistema di carrelli a guida autonoma movimenta i semilavorati e i componenti dal magazzino automatico alle celle di produzione, sotto il controllo di un calcolatore. Infine, le sei celle di produzione (lavorazione o assemblaggio) sono alimentate dal magazzino automatico; ciascuna è dotata in input di un proprio buffer per semilavorati-componenti. Fra i principali obiettivi che il sistema intende perseguire: garantire rifornimenti puntuali e pertinenti alle celle di produzione, in quanto i tempi relativi alle movimentazioni sono drasticamente ridotti (la gestione informatizzata permette l’invio di alert e segnalazioni che aiutano a prevenire il rischio di stockout o sovra-giacenze, riducendo i tempi e i costi di replenishment); ridurre il material handling e assicurare massima protezione per le merci e le persone, minimizzando il rischio di infortuni; ridurre l’ingombro a pavimento. La messa in funzione del sistema comporta la progettazione dell’ottima politica di gestione delle scorte, ossia la definizione di quantità e tempistiche del riordino di ciascun articolo. In tal senso, si osserva che la dislocazione della scorta di un dato articolo nel magazzino centrale o in quello automatico da un punto di vista logico non fa differenza. Tuttavia, è rilevante stabilire la frazione della scorta complessiva disponibile nel magazzino automatizzato, poiché essa è la sola che gli Agv possono prelevare per alimentare le celle di lavorazione. La scorta deve, pertanto, essere gestita in una logica di replenishment. La gestione del magazzino automatizzato non è legata a ciò che accade in quello centrale, dove si mira fondamentalmente a stabilire la frequenza degli ordini verso i fornitori esterni e la quantità da approvvigionare. Come detto, entrambi costituiscono, in effetti, un unico magazzino logico. Inoltre, allo stato attuale, non sono state registrate particolari criticità nella gestione pregressa del magazzino centrale e, anche sulla base di analisi svolte insieme con l’azienda, si ritiene che tale condizione permanga anche con l’introduzione del magazzino automatico. Pertanto, si è ritenuto realistico semplificare le ipotesi di studio assumendo che il magazzino centrale assicuri a quello automatizzato l’alimentazione richiesta. Ciò consente di porre il focus dell’analisi sulla gestione di quest’ultimo. In particolare, questo tema è rilevante in quanto il costo per unità di volume nel magazzino automatizzato è superiore a quello di uno convenzionale. Tale considerazione è determinante nel comprendere il valore dell’innovazione teorica proposta.L’articolo integrale è pubblicato sul numero di Settembre 2022 di Sistemi&Impresa.
Per informazioni sull’acquisto di copie e abbonamenti scrivi a daniela.bobbiese@este.it (tel. 02.91434400)