Intervista a Luca Ceppi, Facility Manager e CIO di Elemaster
Internazionalizzazione, evoluzione dei sistemi informativi e implementazione del software J-Flex MES di Tecnest: le strade intraprese dal produttore di schede e apparati elettronici high tech
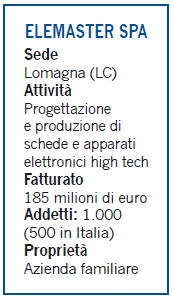
Fondata nel 1978, Elemaster è diventata una delle più importanti società ODM-EMS in Europa. Oggi Elemaster è il punto di riferimento per lo sviluppo competitivo dei propri clienti, attraverso i suoi servizi di design, engineering e realizzazione sia di schede elettroniche sia di dispositivi completi, integrati con la produzione di componenti custom e la produzione di PCB.
Nel corso del 2015 Elemaster è cresciuta raggiungendo un fatturato consolidato di circa 185 milioni di euro, e impiega mille persone nel mondo.
Oggi Elemaster è sul mercato ODM-EMS come un one-stop-shop per i propri clienti, che sono i principali attori globali nei settori ad alto contenuto tecnologico come l’elettro medicale & healthcare, il settore ferroviario e dei trasporti, l’avionica e la difesa, l’high tech mobility, il settore industriale ed energy.
Quasi 40 anni di esperienza e continui investimenti hanno dotato Elemaster di un know-how consolidato nella gestione di componenti avanzati come BGA, μBGA, Flip-Chip, e la produzione Rohs compliant. Ciascuno dei 6mila diversi tipi di prodotto che Elemaster produce ogni anno è il risultato di una soluzione tecnologica taylor-made.
Elemaster, con l’headquarter in Italia (nei pressi di Milano) e stabilimenti di produzione in Tunisia (Bizerte), Usa (Atlanta), India (Chennai) e Cina (Shanghai), supporta i propri clienti a livello mondiale. L’azienda ha sempre adottato una politica di investimenti per il futuro: il più recente esempio di questa prospettiva è l’acquisizione di CAD-UL, una società tedesca localizzata a Ulm e specializzata nei servizi di ricerca e sviluppo, PCB layout e prototipazione e produzione di piccole serie per l’area D-A-CH. Sistemi&Impresa ha incontrato Luca Ceppi, Facility Manager e CIO di Elemaster, che, rispondendo ad alcune domande ha illustrato la trasformazione in atto della società e i progetti di innovazione attuali e futuri.
In questo periodo si parla molto di quarta rivoluzione industriale e di nuove tecnologie per rendere più competitivo il sistema industriale italiano. Dal vostro punto di vista come sta cambiando l’industria in Italia? Quali sono le opportunità e le criticità legate all’adozione di queste nuove tecnologie?
Dall’industria “pesante” all’industria “pensante”: è questa la trasformazione che l’industria manifatturiera Italiana sta vivendo e sulla quale deve assolutamente puntare per riprendere il terreno perduto ceduto ai Paesi in via di sviluppo negli ultimi decenni. Per supportare questo processo è fondamentale che la nostra impresa sia flessibile e veloce nel cambiamento utilizzando la digitalizzazione per dare risposte rapide al mercato. Questa rivoluzione digitale potrebbe portare nuova occupazione nelle nostre aziende che l’introduzione dei robot degli Anni 70 aveva notevolmente ridotto. Sarà però un’occupazione di tipo diverso, si creeranno nuove figure professionali a oggi ancora non presenti, insomma un’occupazione di una maggiore qualità. Questo è l’obiettivo: scegliere l’anello “immateriale” della catena del valore che è più leggero e flessibile, altrimenti il rischio è di rimanere ancorati agli anelli pesanti a minor valore aggiunto.
Il Governo ha recentemente annunciato il nuovo Piano Nazionale per l’Industria 4.0. Cosa pensa di questa iniziativa e quali possono essere gli impatti e i reali vantaggi per una realtà industriale come la vostra?
L’iniziativa del Governo è fondamentale affinché si crei quel microtessuto di conoscenze che possono portare alla formazione delle nuove professionalità di cui parlavo pocanzi.
Il prodotto fisico, oggi, prima ancora di essere materiale è “dato informatico” e come tale è assolutamente necessario saperlo “trattare”.
Ancora di più, domani, saremo coinvolti nella gestione di dati: prima, relativi alla creazione degli oggetti fisici, poi, da quelli forniti dagli stessi oggetti attraverso sensori di ogni natura e microprocessori (piccoli cervelli) presenti a bordo dei prodotti. Già oggi alcune università offrono nuovi corsi di laurea volti alla creazione di queste nuove figure professionali, per esempio l’Università Luigi Bocconi ha presentato proprio quest’anno Bemacs, un nuovo corso di laurea per interpretare i Big data attraverso le lenti dei modelli economici.
Da queste nuove figure la nostra azienda non potrà che trarne vantaggio per poter offrire ai nostri clienti servizi sempre più moderni e adeguati alle nuove tecnologie. Già oggi nostri prodotti progettati e costruiti per i nostri clienti sono basati su sensori che dialogano tra di loro e interpretano le informazioni raccolte per poi fornire diversi scenari su cui prendere una decisione.
In tema di innovazione e di Industria 4.0 qual è la vostra strategia e cosa in concreto state facendo?
Elemaster sta vivendo in questi anni un processo di trasformazione trasversale che parte dall’internalizzazione alla trasformazione dei propri sistemi informatici.
Dal 2012 abbiamo aperto stabilimenti produttivi negli Stati Uniti, in Cina e in India; l’intento non è quello di delocalizzare le produzioni in altri Paesi bensì quello di seguire i nostri clienti e fornire loro gli stessi prodotti e servizi ovunque essi ne abbiano bisogno: “We are where you are” è la nostra filosofia.
Infatti l’headquarter è e rimane in Italia, ed è in quest’ottica che i servizi IT vengano governati e forniti dalla sede centrale. A partire dal 2009 è stato avviato un progetto di rivoluzione dei nostri sistemi informatici; innanzitutto abbiamo rinnovato la nostra piattaforma hardware rivolgendoci al “cloud on premises” sostituendo i nostri vecchi server con soluzioni blade e sistemi di virtualizzazione.
Questo ha permesso da subito, grazie alla scalabilità di questa struttura, la possibilità di fornire nuovi servizi on demand e time to market contribuendo così a velocizzare i passaggi successivi del progetto. Successivamente il programma prevedeva la sostituzione dei vecchi strumenti informatici (PLM ed ERP) con soluzioni multinazionali e, soprattutto, web-based; in questo modo le aziende che sarebbero nate successivamente avrebbero potuto essere connesse al “cloud di Elemaster”.
Come rientra in questa strategia il progetto realizzato con Tecnest?
Il progetto Tecnest nasce da un duplice scopo: l’installazione del nuovo ERP – ancora in parte in fase di completamento – interconnesso alla necessità di migliorare l’efficienza dei nostri processi e la pianificazione aziendale.
In concreto cosa ha fatto Tecnest per risolvere le vostre problematiche?
Con Tecnest abbiamo disegnato insieme un piano di implementazione del loro software J-Flex MES (Manufacturing Execution System) che parte dalla raccolta dei tempi di ogni singola fase del processo, attraverso la completa gestione dello shopfloor con palmari e dispostivi user friendly, fino alla raccolta dei dati di qualità di ogni singolo pezzo prodotto.
Una parte fondamentale di questo progetto ha portato a interfacciare le nostre macchine di produzione e di test con J-Flex, l’obiettivo è quello di raccogliere i dati forniti dalle linee automatiche, interpretarli e aumentare l’efficienza degli impianti. J-Flex infatti riceve in tempo reale dalle linee di produzione i dati relativi a quantità prodotte e tempi e, in caso di eventuali errori, invia un alert via email ai responsabili per poter prendere opportune azioni correttive. I dati raccolti sono a disposizione dei supervisori e dei singoli operatori in J-Flex attraverso dashboard con grafici e Kpi di sintesi.
Un altro aspetto fondamentale gestito dal software di Tecnest è la tracciabilità e rintracciabilità in produzione. Attraverso l’utilizzo di codici univoci e la definizione di opportune unità di gestione logistica dei materiali, il sistema J-Flex MES genera i legami di tracciabilità dalle materie prime al prodotto finito (e viceversa) con riferimento sia ai lotti dei materiali utilizzati sia alle risorse produttive impiegate durante il processo (macchina e manodopera). Attraverso una gestione delle locazioni, inoltre, il sistema permette di capire in ogni momento dove è ubicata ciascuna unità all’interno dello stabilimento. Oggi, grazie al sistema J-Flex e allo shopfloor client JET, installato su oltre 200 postazioni di reparto e una quarantina di palmari, conosciamo l’esatta posizione di ogni singola scheda presente in azienda e il tempo esatto di quanto abbiamo impiegato per produrla.
Perché avete scelto Tecnest? Quali i plus dell’offerta?
Elemaster non sceglie i propri fornitori solo in base all’offerta economica: in Tecnest abbiamo visto e poi trovato un partner che ha “capito” le necessità della nostra azienda e le ha fatte sue studiando e portando soluzioni calzate sulle nostre esigenze.
Quali i vantaggi, quantitativi e qualitativi, conseguiti con l’implementazione della soluzione Tecnest?
Questo progetto ha permesso di ottimizzare i tempi ciclo e di poter individuare i colli di bottiglia lungo il processo, così da permetterci di ottenere una maggiore efficienza pari al 20%.
Grazie alla gestione della tracciabilità in produzione, inoltre, abbiamo visibilità su tempi, materiali e risorse utilizzate per realizzare ciascun prodotto, possiamo capire esattamente dove è ubicato e risalire alla fonte di eventuali problemi segnalati a ogni livello della filiera produttiva.
Naturalmente il processo è iterativo e non si ferma mai. In azienda abbiamo un team che si dedica a tempo pieno all’analisi dei dati settimanali e che, in ottica di Lean manufacturing, svolge le azioni correttive necessarie. Inoltre, ogni settimana, vengono introdotti decine di nuovi prodotti per i quali, attraverso processi strutturati di NPI, devono essere verificati i tempi di produzione, corretti i cicli e rilasciati per la mass production.
Quali saranno i prossimi passi della società in ottica innovazione?
La “generazione Z”, i nati con lo smartphone, è ormai giunta nelle aziende. Se per la nostra generazione la grande rivoluzione è stata l’email, i ragazzi di oggi quasi non sanno che cos’è. Pochi di loro ne posseggono una privata. Oggi il loro modo di comunicare è completamente diverso, utilizzano Facebook, WhatsApp…
Le email diventeranno presto antiquate anche all’interno degli ambienti lavorativi. È per questo motivo che uno dei prossimi passi sarà quello di implementare una piattaforma di social collaboration completamente integrata con l’ERP e la Business Intelligence. In questo modo l’efficienza della comunicazione interna sarà molto più rapida e l’utente non dovrà crearsi le informazioni che gli interessano tramite query o estrazioni varie dall’ERP, ma saranno già presenti nei cruscotti sulla sua homepage di accesso ai sistemi informatici aziendali. Inoltre abbiamo avviato un progetto che, partendo dall’acquisizione della società tedesca CAD-UL, attraverso l’utilizzo di nuove tecnologie di produzione rapida, come screenprinting e additive manufacturing, porterà il gruppo a offrire nuovi servizi di prototipazione rapida e di preserie in tempi molto contenuti.