Chi usa l’additive manufacturing? Pale, pasta e tutori ortopedici in 3D
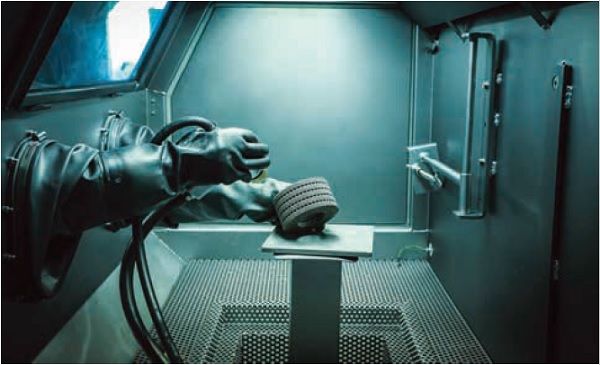
Abbiamo incontrato tre aziende in settori completamente differenti per farci raccontare come utilizzano la stampa 3D per il loro business.
Si tratta di Avio Aero, Barilla e Officine Ortopediche Rizzoli
di Luca Bastia
Un mercato mondiale previsto per il 2020 di quasi 18 miliardi di dollari, sono le stime fatte dagli analisti di Context riguardo al segmento Stampa 3D, prendendo in considerazione anche i materiali di consumo e i sevizi.
Considerando solo il giro d’affari delle stampanti la crescita è prevista dagli 1,8 miliardi di dollari stimati per quest’anno a 6,4 nel 2020 mettendo insieme stampanti professionali e non.
Secondo Context la stampa 3D è molto diffusa nel segmento della prototipazione rapida, ma ha ancora molta strada da fare nel manufacturing, anche se non mancano esempi di utilizzo. Qui di seguito raccontiamo tre esperienze in settori differenti in ambito manifatturiero.
Il caso Avio Aero. La stampa di parti di motore
Avio Aero, 4.000 dipendenti e circa 2 miliardi di fatturato, fa parte di General Electric e in particolare della divisione GE Aviation, è una società che si occupa di componenti destinati ai motori aerei civili e militari. In particolare, l’azienda è leader a livello mondiale nella produzione di turbine di bassa pressione e trasmissioni meccaniche. Dunque componenti di motori destinati alla propulsione aeronautica. Per realizzare queste componenti Avio Aero si avvale, oltre che delle tecnologie di produzione tradizionale, anche dell’additive manufacturing, meglio nota come stampa 3D, che quindi viene utilizzata per creare alcuni dei prodotti che rappresentano il core business dell’azienda.
“Più precisamente”, spiega Paolo Gennaro, Additive manufacturing Product Leader, “sulle turbine stiamo sviluppando e abbiamo in produzione le pale della palettatura rotorica e alcune parti della turbina; per la trasmissione stiamo sviluppando gli hausing, cioè la struttura della trasmissione; e per i combustori i fuel nozzle, componenti all’interno del combustore che servono a miscelare combustibile e comburente”.
L’additive manufacturing viene utilizzato a partire dalla realizzazione del prototipo plastico per le verifiche di ingombro e per presentare il prodotto ai vertici aziendali, successivamente viene fatta una preserie prototipale per lo sviluppo prodotto (in questo caso con l’utilizzo di materiale metallico) e poi viene avviata la produzione in 3D.
“Se si progetta un prodotto per essere realizzato in additive poi va prodotto con la stessa tecnologia, non si potrebbe produrlo diversamente. Un altro conto è fare un prototipo in additive che poi verrà realizzato in fonderia o con altre tecnologie (asporto), in questo caso si perde tutto il vantaggio del design for manufacturing”, precisa Gennaro. “Mentre progettando il componente con la finalità di essere prodotto in grande serie con tecnologia additive, la susseguente produzione con questa tecnologia mantiene numerosi vantaggi; riduzione dei costi, migliore qualità e prestazioni del componente”.
La stampa 3D in Avio Aero è entrata già dal 2004.
C’erano già dei materiali adatti per la vostra produzione?
No. Li abbiamo sviluppati al nostro interno.
Uno sviluppo durato una decina d’anni.
Ed è dal 2004 che avete iniziato la produzione in serie?
No, non da subito, c’è stato un periodo di sviluppo. Abbiamo iniziato con la prototipia, lo sviluppo del design e lo sviluppo dei materiali e, solo recentemente, si è potuto iniziare una produzione di serie, perché per arrivare a questo bisogna avere un design validato, dei materiali completamente caratterizzati e aver anche costruito la fabbrica.
Le macchine da stampa 3D le trovate sul mercato o anche queste le avete progettate al vostro interno?
In molti casi sono macchine ottimizzate e customizzate sul nostro prodotto, sono sistemi che abbiamo sviluppato insieme al fornitore.
Avete verificato il vantaggio di utilizzare l’additive manufacturing piuttosto che la produzione tradizionale?
Ovviamente sì. Ci siamo chiesti perché farlo in additive? E la risposta è che se si sfruttano tutti i vantaggi della progettazione fatta in 3D, con un design specifico, si ottengono prestazioni migliori in termini di performance del motore e di risparmio di peso; tutto ciò che vola più è leggero meglio è.
Il fatto di realizzare le parti in additive consente di realizzare dei componenti più leggeri, ma anche più performanti. Si riesce ad aumentare il valore del prodotto e a ridurre i consumi.
additive manufacturing, avio aero, barilla, officine ortopediche rizzoli, stampa 3D